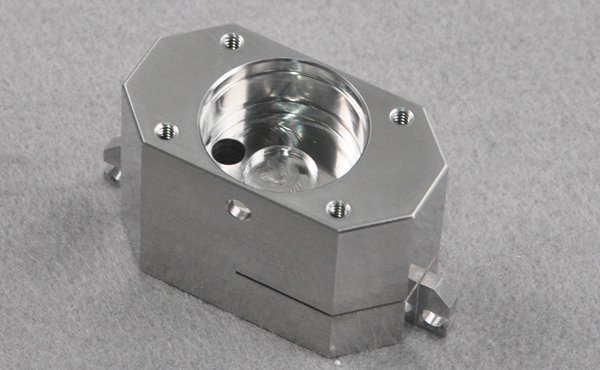
Stainless steel’s versatility makes it a material of choice in a wide range of applications, from industrial and high-tech sectors to consumer products and healthcare. The specific grade and finish of stainless steel can be tailored to meet the requirements of each application. CNC machining is a common method to make parts out of stainless steel. Here are some tips to CNC machining stainless steel parts.
CNC machining stainless steel can be challenging due to the material’s hardness and tendency to work-harden, which can cause tool wear and reduced machining efficiency. Here are some tips for CNC machining stainless steel effectively:
- Select the Right Stainless Steel Alloy: There are various stainless steel alloys, each with different properties. Choose the alloy that best suits your application in terms of corrosion resistance, strength, and machinability.
- Tool Selection: Use high-quality cutting tools designed for stainless steel machining. Carbide tools with sharp cutting edges are commonly used. Coated tools, such as TiAlN or TiCN-coated carbide, can help reduce wear.
- Cutting Speed and Feeds: Optimize cutting speeds and feeds for stainless steel. Stainless steel usually requires slower cutting speeds and higher feed rates compared to other materials. Consult your tool manufacturer’s recommendations and adjust based on the specific alloy.
- Coolant and Lubrication: Stainless steel machining generates heat, so it’s crucial to use a coolant or cutting fluid to dissipate heat and improve tool life. Water-soluble coolants or specialty cutting fluids designed for stainless steel are often used.
- Toolpath Strategy: Use appropriate toolpath strategies to minimize tool engagement and avoid overheating. Consider climb milling to reduce tool deflection.
- Minimize Runout: Ensure that the CNC machine spindle and toolholder have minimal runout. Excessive runout can lead to tool wear and poor surface finish.
- Workholding: Secure the stainless steel workpiece properly using the right workholding devices, such as vises, clamps, or fixtures. Stiff and rigid workholding is essential to prevent vibration and movement during machining.
- Depth of Cut: Use shallow depth-of-cut passes to reduce cutting forces and avoid excessive tool wear. Multiple shallow passes are often more efficient than a single deep cut.
- Chip Control: Stainless steel can generate long, stringy chips that can cause problems. Use chip breakers or peck drilling to manage chip control effectively.
- Tool Inspection: Periodically inspect the cutting tool for wear and damage. Replace or re-sharpen the tool as needed to maintain consistent machining quality.
- Machine Rigidity: Ensure that your CNC machine is in good working condition, and that it provides the necessary rigidity for stainless steel machining.
- Quality Control: Regularly inspect the machined stainless steel parts to check for dimensional accuracy, surface finish, and any defects. Make sure they meet the required tolerances and quality standards.
- Safety Measures: Follow safety guidelines when working with CNC machines and stainless steel, and wear appropriate personal protective equipment.
- Post-Machining Processes: Consider any necessary post-machining processes like passivation, pickling, or surface treatments to enhance corrosion resistance and improve the appearance of the stainless steel part.
CNC machining stainless steel requires precision and careful attention to the details mentioned above to achieve high-quality results. It’s essential to adapt machining parameters to the specific grade of stainless steel you are working with, as different alloys may have different machining characteristics. If you have questions, welcome to contact Xielifeng Tech, a reliable CNC machining service supplier in China