The Impact of Assembly Robots on US Manufacturing
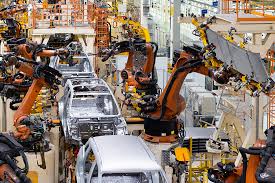
The integration of assembly robots into manufacturing processes marks one of the most significant advancements in modern industry. These machines, designed to perform repetitive and precise tasks, have transformed the landscape of manufacturing in the United States. From improving efficiency to influencing economic factors and quality control, assembly robots are reshaping how products are made.
Economic Implications
One of the most notable benefits of assembly robots is their ability to significantly boost productivity. Robots can operate continuously without the need for breaks, fatigue, or downtime, leading to higher output and efficiency. For example, a single robot can often perform the work of several human workers, resulting in increased production rates and reduced lead times. Quantitative studies have shown that companies integrating robots into their manufacturing processes often see productivity improvements of up to 30%, which can translate into substantial cost savings and higher profit margins.
Cost Reduction
While the initial investment in assembly robots can be substantial, the long-term cost benefits are significant. Over time, robots can reduce labor costs, minimize waste, and lower maintenance expenses. The automation of repetitive and hazardous tasks also reduces the likelihood of workplace injuries, leading to further cost savings. Comparing the long-term costs of robotic systems with ongoing labor expenses, many companies find that the return on investment justifies the initial expenditure.
Impact on Employment
The introduction of assembly robots has sparked debates about their impact on employment. While robots can displace certain manual jobs, they also create opportunities for new roles in robot maintenance, programming, and system integration. The shift towards a more automated workforce necessitates a focus on reskilling and upskilling programs to prepare workers for these new roles. Additionally, the increased productivity and competitiveness of companies using robots can lead to business expansion and the creation of new job opportunities in the long run.
Quality and Precision Improvements
Assembly robots have revolutionized the quality of products manufactured. With their ability to execute tasks with exceptional precision, robots significantly reduce errors and defects. This improvement in product quality is especially crucial in industries where tolerances are tight and quality standards are high, such as in electronics and aerospace. The consistent and repeatable performance of robots ensures that each product meets stringent quality standards, leading to fewer returns and higher customer satisfaction.
The advancements in robotic technology have enabled unprecedented levels of precision in manufacturing. Modern robots can perform intricate assembly tasks with micron-level accuracy, which is essential for producing complex components and assemblies. This precision engineering capability allows manufacturers to achieve higher levels of detail and complexity in their products, driving innovation and meeting the evolving demands of the market.
Innovation and Competitive Advantage
Assembly robots are not only enhancing current manufacturing processes but also driving innovation in product design and development. The flexibility and adaptability of modern robots allow manufacturers to experiment with new designs and materials that were previously difficult or impossible to handle. This ability to innovate enables companies to create cutting-edge products and stay ahead of the competition. For example, the use of robots in prototyping and testing phases can accelerate the development of new technologies and products.
In the global manufacturing arena, US companies leveraging assembly robots gain a competitive edge through increased efficiency, reduced costs, and improved product quality. The adoption of advanced robotics technologies positions US manufacturers as leaders in high-tech, precision-driven industries. This competitive advantage is crucial for maintaining a strong presence in international markets and responding to global competition effectively.
Challenges and Considerations
The cost of purchasing and integrating assembly robots can be a significant barrier for many companies, especially small and medium-sized enterprises (SMEs). The initial investment includes not only the cost of the robots themselves but also the expenses associated with system integration, programming, and training. To manage these costs, manufacturers can explore financing options, government grants, and phased implementation strategies that allow for gradual investment in robotics.
Integration with Existing Systems
Integrating robots into existing manufacturing systems presents its own set of challenges. Compatibility issues between new robotic systems and legacy equipment can complicate the integration process. To address these challenges, manufacturers should work with experienced system integrators and invest in technology that facilitates seamless integration. Best practices include conducting thorough feasibility studies, developing comprehensive integration plans, and ensuring that all systems are compatible and interoperable.
Workforce Reskilling and Training
The adoption of assembly robots necessitates a shift in workforce skills. Workers need to be trained in robot operation, programming, and maintenance to support the new automation systems. Reskilling programs and educational initiatives play a crucial role in preparing the workforce for these changes. Companies can partner with educational institutions and training organizations to develop programs that address the specific needs of their operations and ensure a smooth transition to a more automated workforce.
Conclusion
The impact of assembly robots on US manufacturing is profound and far-reaching. From enhancing productivity and quality to driving innovation and providing a competitive edge, these machines are reshaping the industry landscape. While challenges such as high initial investment and workforce reskilling remain, the benefits of robotic integration are clear. As technology continues to advance, the role of assembly robots will only grow more significant, paving the way for a more efficient, innovative, and competitive manufacturing sector in the United States.
For those interested in exploring advanced robotic solutions, Universal Robots offers a range of cutting-edge technologies designed to enhance manufacturing processes and drive industry innovation. Embracing these advancements will be key to staying at the forefront of the evolving manufacturing landscape.